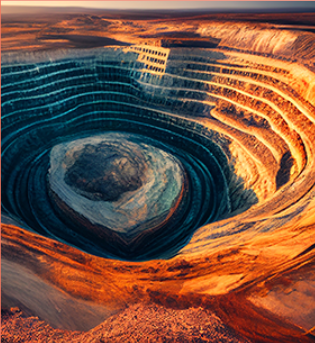
Technology can have unpredictable consequences. So discovered Rio Tinto when, in 2017, it introduced autonomous operations to its Rio’s Hope Downs 4 mine, in the Pilbara region of Western Australia.
Equipment at the mine could be controlled by engineers remotely, two hours flight away at its operations centre in Perth. While productivity surged, the engineers were unaccustomed to their new sterile environment. “You have to blow dust in their faces to make them feel like they are in Pilbara,” one executive joked.
This trail-blazing initiative aside, the implementation of technology into mining operations has been famously slow.
Many operators understand the value of digital asset management solutions. But the realities of the sector – the boom-and-bust cycles, the volatility and labour shortages – mean long-term strategies that look to digital and modern methods of working, are frequently pushed down the corporate agenda.
The focus, instead of implementing asset performance management improvement strategies, has been on reacting to daily production needs and demands.
Now, however, mining leaders are increasingly recognising that digital solutions are the only route to managing the swathe of pressing challenges they face.
These challenges include the need to extract in a way which minimises environmental impact and reduces water and energy use; the drive for better safety performance; the rising cost of labour and equipment; and the pressure to mine responsibly and with full consideration for local communities.
The cost and time implications of these to doing business means that this sector – so critical to the world’s daily activities – has left leaders with little option but to consider long-term digital programmes.
They know that these will support them in better managing their assets and facilitating the lowest, risk-managed, cost of conversion of ore to product not just this month, but next quarter and next year.
Shaking off the short-term approach
In mines across the globe the impacts of short-term asset management strategies and lack of technology implementations are evident. They include:
- Siloed data held in disparate systems meaning workers spend 30 per cent of their days or more searching for information, tools and parts;
- Under-utilisation of critical mining equipment due to frequent unplanned maintenance and breakdowns hitting overall productivity;
- Management by manual processes and Excel making agility and reactiveness a near impossibility.
Reactive maintenance practices are leading to higher maintenance costs, while a lack of integrated data systems is resulting in inefficiencies due to the difficulty in tracking asset performance and managing inventories.
The costs of unreliability are multiple. They include the lost value of the asset while it is unavailable, the cost of repairing equipment after failure and the cost of energy consumed while shutting down and re-starting. There is also the loss of production with equipment failing in the ore face with its process partly completed.
Introducing sustainable asset management changes – changes that stick
To produce sustainable results, any modern, digital enterprise asset management strategy must address the full lifecycle of the assets. Not only the technology stack but also the business processes across multiple departments (enabling software alone is never a fix).
This holistic approach will identify where the key opportunities lie to enhance operational efficiency, reduce downtime and optimise maintenance strategies.
Key initiatives to consider for any mining organisation today are predictive maintenance technologies and practices and asset management software. Connecting up and integrating siloed data through the establishment of a data strategy is critical to gaining full control over your assets and driving peak performance, all the time.
Maintenance teams need the training and education necessary to ensure digital programmes are effective and have long-term, sustainable impacts.
Success should be defined and KPIs established to enable new asset management and reliability practices to be regularly evaluated and continuously improved.